Raymond Mill Machine Manufacturing
As a production line for grinding non-metallic minerals, the Raymond mill machine is commonly used in coal mines, metallurgy, and mines with a Mohs hardness of less than 9.3 and a humidity below 6%. In addition to its simplicity, convenient maintenance, easy operation, high production efficiency, low energy consumption, and adjustable particle size and fineness, the Raymond mill can be used in various industries.
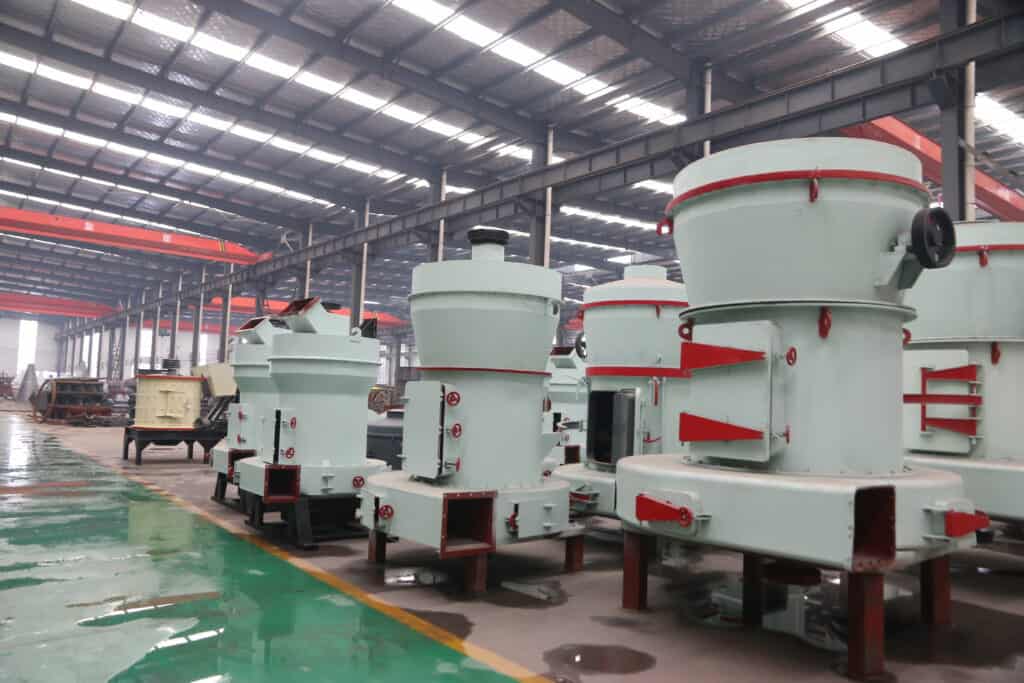
What Is Raymond mill Machine?
Raymond mills work by using friction between the grinding roller and the grinding ring to grind the material to a fine powder. They’re advanced mill equipment. For powdering ores, ash, gypsum, feldspar, cement, refractory materials, and other stuff, it’s used in building materials, chemical industry, metallurgy, electric power, and other industries.
It’s easy to maintain, easy to operate, has high work efficiency, low energy consumption, etc., and you can adjust particle size and fineness during processing, according to your needs.
Designed for big, medium, and small mines, the chemical industry, building materials, metallurgy, etc., the R-type Raymond mill is a closed loop, high-fine milling machine. The fineness uniformity of the powders produced by the mill can reach 95% of the required fineness, that is, the sieve can reach 95%. With its vertical structure as a whole, the Raymond mill is extremely complete. It can form a production system all on its own.
Compared to traditional mills, the Raymond mill grinds 80-400 mesh powders. It’s an updated version. In terms of reliability, safety, stability, cost-effectiveness, grinding efficiency, and classification accuracy, the equipment is reliable, safe, stable in performance, and affordable. It is a special powder grinding equipment that you can adjust between 80 and 400 mesh. The fineness can be adjusted by the customer based on their needs.
My sincere recommendation for Dura Mortar to overseas friends!
During the past 7 years, Raymond mill machine has worked so stable, and its main structure hasn't broken, except for its wearing part. That's amazing to us and we'd definitely recommend it to other overseas friends!
Raymond mill grinding machine applications
After years of improvement and innovation, and different materials and needs of different customers, Raymond Mill will now work with most materials, and the finished product will be between 613 m and 44 m in size. The analyzer and fan work together to meet the needs of different users, such as calcium carbonate processing, gypsum powder processing, power plant desulfurization, non-metallic ore pulverization, coal powder preparation, etc.
The composition of the mill production line:
The mill production line usually includes hammer crusher, bucket elevator, storage bin, vibrating feeder, micro-powder mill host, frequency conversion classifier, double cyclone powder collector, pulse dust removal system, high-pressure fan, air compressor, electrical control system, etc. The feed particle size (about 1cm) of a large piece of material is crushed with a hammer crusher, then adjusted to fit the mill’s requirements by adjusting the mill analysis machine speed, and then manually packed into bags. You can also choose between different types of mills and configure automatic micropowder balers.
Machine maintenance:
After the Raymond mill has been used for a period of time, it needs to be overhauled, and at the same time, the wearing parts, like the grinding roller, grinding ring, blade, etc., need to be overhauled and replaced. In addition to checking for looseness and lubricating grease, we have to check the connecting bolts and nuts of the grinding roller device before and after use.
A grinding roller generally doesn’t last more than 500 hours, so it should be replaced when it reaches its limit. It’s important to clean the roller sleeve’s rolling bearings on a regular basis, and to replace damaged parts whenever possible.
Fineness is adjusted by adjusting the analyzer. When we use the mill, it might be different. Depending on the size, hardness, moisture content, specific gravity, and processing thickness of the material, we can adjust the fineness of the finished product. A fast speed means a high fineness, and a slow speed means a low fineness.
When you’re shutting down, stop the feeding first, and then stop the main machine. When you stop the machine, stop the feeding, but make sure the main engine keeps running so residual abrasives can be milled. The main motor and analyzer motors can be turned off after about one minute, then the fan motor can be turned off to facilitate blowing. Net residual powder.
Raymond mill failure: how to prevent it?
1. Raymond mills produce less powder?
This is mostly because the powder locker isn’t tightly sealed. You’ll get no powder or less powder output during the milling process if the powder locker seal isn’t done properly, so check the seal of the powder locker and adjust the degree of sealing.
2. Is it too fine or too coarse?
This is where the analysis engine does not work. The analysis engine is responsible for analyzing the size of the finished powder, whether it meets the finished product standard, and if it must be further sanded. When the blades of an analysis machine are severely worn, they cannot perform the function of classification, causing the powder to be too fine or too coarse. In such cases, a new blade can be installed to resolve the problem.
3. Does the powder particle size appear to be abnormal?
There is an incorrect adjustment of the Raymond mill fan. A Raymond mill fan will produce abnormal powder output if the air volume is not adjusted properly. For example, if the air volume is too large, the powder output will be too thick, and if the air volume is too small, the powder output will be too fine. When abnormal circumstances occur, it may be necessary to adjust the air volume of the fan to correct the particle size of the powder.
4. A gap exists between the powder leakage at the bottom of the mill and the edge of the milling disc.
The baffle may be designed to recycle the material return device or block the material leakage device, or to increase the distance between the outer edge of the material bed and the outer edge of the grinding table.
5. Vibration of the fan is excessive.
The accumulation of powder on the blades or unbalanced wear on the blades, or loose anchor bolts will cause excessive fan vibration. In particular, we can adjust fan vibration by removing the powder accumulation on the blades or replacing the blades, and tightening the anchor bolts.
Working with A leading raymond mill machine manufacturer as Dura Mortar
By choosing the Raymond mill equipment provided by Dura Mortar, you can increase production capacity by more than 40%, reduce energy consumption by more than 30%, improve market competitiveness, and increase grinding efficiency;
Scientific design and structure can contribute to positive economic and social outcomes, as well as keeping the production workshop clean and tidy. In addition to providing environmental protection requirements and providing your workers with safe and clean working conditions, it is equipped with a pulse dust collector that can achieve 99% efficiency of dust collection.
Having A Project! We have you covered!
"Take the first step towards a successful dry mortar plant project and contact us now for expert guidance and support!"